SMART project engages regional stakeholders in Jashore
To foster regional stakeholders’ engagement and promote sustainable practices among microenterprises in Jashore, the Sustainable Microenterprise and Resilient Transformation (SMART) project of Palli Karma-Sahayak Foundation (PKSF) conducted a series of workshops and consultations in Jashore from 19-20 November 2024.
On 20 November, a workshop at the RRF Conference Room brought together a diverse group of participants, including government officials, academicians, and representatives from Partner Organizations (POs). Eun Joo Allison Yi, Task Team Leader of the SMART project from the World Bank, underscored the critical role of stakeholder collaboration in achieving the project’s goals. She highlighted global examples of Resource-Efficient and Cleaner Production (RECP) practices, emphasizing their relevance to Bangladesh.
Highlighting the need for sustainable solutions, Professor Mohammad Mahfuzur Rahman from Jashore University of Science and Technology advocated for life cycle-based approaches to address the unique challenges faced by microenterprises, emphasizing the need for long-term sustainable solutions. The session was inaugurated by Gokul Chandra Biswas, Project Coordinator of the SMART project of PKSF, with Philip Biswas, Executive Director of the Rural Reconstruction Foundation (RRF), delivering closing remarks.
The workshop featured representatives from government agencies such as the District Livestock Office, Department of Fisheries, Department of Environment, and Department of Agricultural Extension. Officials from PKSF, the World Bank, and six POs—including Rural Reconstruction Foundation, Shishu Niloy Foundation, Jagorani Chakra Foundation, Unnayan Prochesta, DESHA Shechsashebi Artho – Samajik Unnyan O Manobik Kallyan Sangstha, and NABOLOK Parishad. Micro-entrepreneurs and distinguished academicians from Jashore University of Science and Technology also contributed to the discussions.
In addition to the stakeholder workshop, a separate event was held at Jashore University of Science and Technology on 20 November to share insights about the SMART project and raise awareness of sustainable practices, specially RECP practices, among the students.
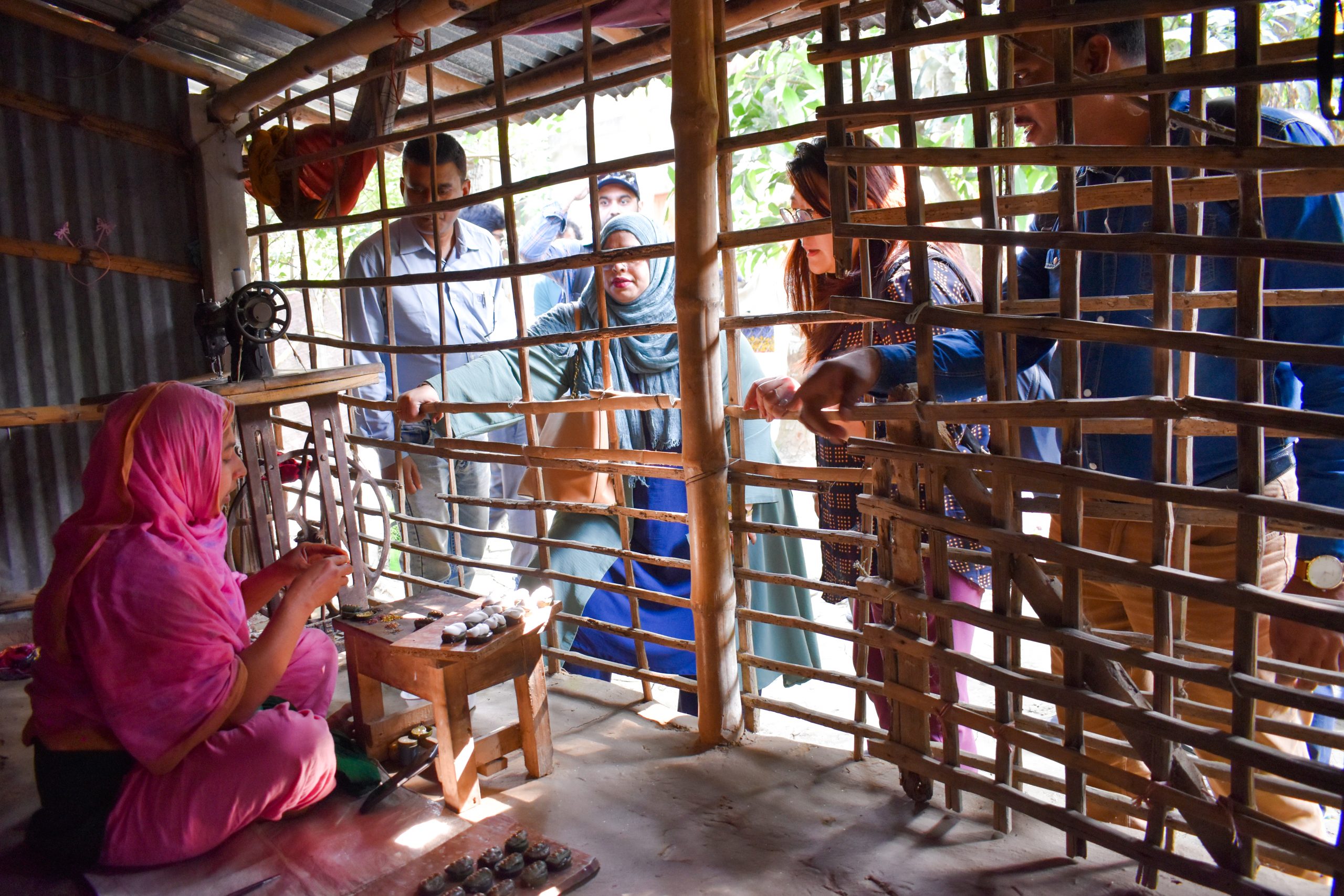
As a part of the two-day itinerary, another consultation meeting was organized earlier on 19 November. Micro-entrepreneurs, and officials of PKSF and its respective POs discussed field-level challenges and opportunities in the meeting. The World Bank team also visited microenterprises in the Automobile and Imitation Jewelry sub-sectors in Jashore and Jhenaidah districts to observe ongoing activities and gather feedback directly from the micro-entrepreneurs on the same day.
The SMART project aims to enhance the environmental sustainability of microenterprises across Bangladesh, targeting 80,000 businesses in the manufacturing, agriculture, and service sectors. By introducing innovative technologies, the project seeks to improve productivity, create jobs, empower women, and foster local economic growth.